Wood Polymer Composites
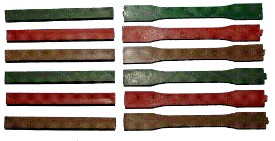
Wood polymer composite test specimens
The use of natural fibers as filler for plastics is rapidly increasing, as it significantly increases the tensile strength, flexural strength and stiffness, while lowering the cost of the resulting composites. At Institute of Wood Science and Technology, we have undertaken a systematic study on synthesis and characterization of wood fiber/flour filled polypropylene(PP) and polyethylene composites(PE). Due to natural fiber's hydrophilic surface, fiber matrix compatibility has been a major problem in developing composites using wood fibers as reinforcements. The quality of interface can be enhanced by introduction of chemical bonds across the interface. This could be achieved either by use of coupling agent or grafting polymer segments on the surface of natural fibers. A novel coupling agent, was synthesized for improving interfacial adhesion between wood and PP, which can overcome some of the limitations associated with conventional coupling agents like MAPP.
The Institute has designed and commissioned a 28mm co-rotating closely intermeshing twin screw extrusion system for melt phase functionalization of polypropylene and for compounding wood fibers with thermoplastic resins. The system design (screw profile, barrel geometries, and screw elements design) is optimized to create a good balance between morphological fineness and filler degrade, thus enabling us to produce composites with excellent mechanical properties. Addition of wood fibers at all levels leads to significant improvement in stiffness, tensile strength and flexural strength with some loss in impact strength. With the wood fiber content in the composite increasing from 10 to 50 wt.%, the tensile strength increased linearly by 45%, while the tensile modulus increased by nearly 200%. Flexural strength exhibited an increase of 85%. The continuous improvement in properties of the composites with the increasing wood filler is attributed to the effective reinforcement of low modulus polypropylene matrix with the high modulus wood filler.
When developing composites form polar wood fibers and non polar polymers, one of the key challenges lies in the successful association of the properties of matrix polymer with those of reinforcing fibers. To overcome the problem of poor dispersion and interfacial adhesion the Institute is working on a novel technique called 'Polymerization-filling technique' (PFT). Using this technique, ethylene was polymerized directly onto the wood fiber surface, and this proved to be an efficient method to promote good filler dispersion and improved adhesion between cellulosic filler and HDPE. Highly filled composites were prepared by filler supported catalyst system using cellulosic materials as fillers in a slurry reactor. Using this novel technique, very high catalyst efficiencies could be achieved with almost no reactor fouling even at very high solid content in the slurry. Kinetic model for ethylene polymerization using filler supported catalyst system was also developed to predict the instantaneous reaction rates.